
The bottom die base is constructed from a piece of 3'x4'x12' tubing and has a 1/2'x3'x4' steel plate welded to the face of it. This allows for the use of 1' tall dies with 1/4' base plates to give you 7 1/2' inches of max working space.

At this point the frame will stand 6' 3' tall with the distance between the ram and the bottom die base being 10'. Nothing special to note here except that that height of the frame can be adjusted to match the user. In this pic you can see a mock up of the frame. The clevis/pin holes for the cylinder are layed out on center of the 1' plate for the top of the press and for the ram.ĭiy Hydraulic Forging PressIt is worth noting that the height of the holes need s to be adjusted to match the clevis's on the cyclinder you use don't trust the manufactures specs. I dont have any pics of cutting or laying out the ram guides ( lost em on accident ) but it's pretty basic stuff. Other hydraulic parts were purchased from Northern Tools.
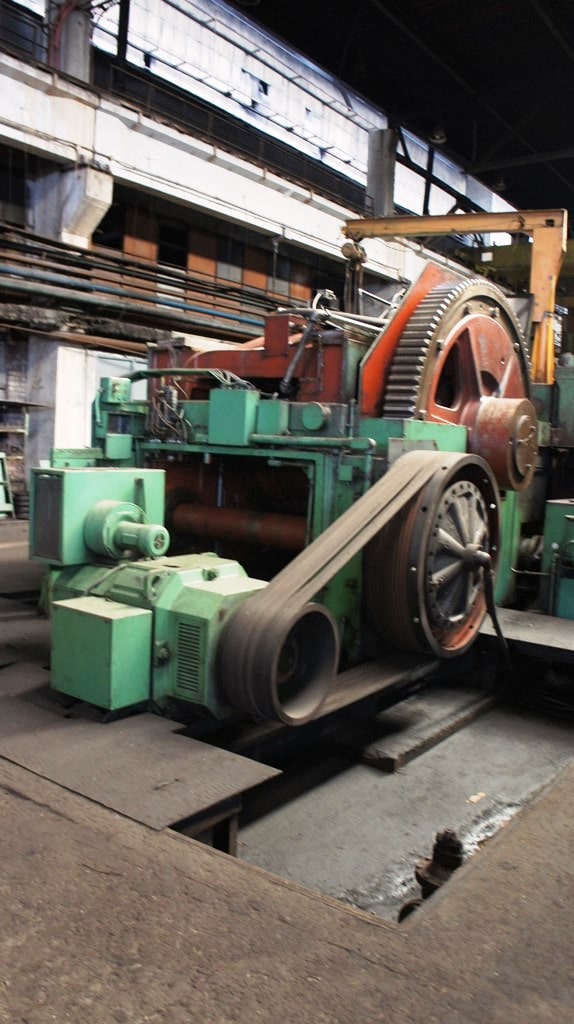
Parts marked with * all came from Surplus Centerand should be adjusted to work with your setup. (2) 1/2'x1/2' male to female right angle swivels* (4) 1/2'x3'x 1 1/2' steel plate (gussets)ĥ' bore x 8' stroke (double acting) 3000 psi cyclinder*ġ0 gallon tank Build Your Own Hydraulic PressĢ0 gpm open center non-dentent control valve* (1) 12' 3'x4' x1/4' walled tubing for bottom/die base (2) 6' 3'x4'x1/4' walled tubing for sides Where I can I've listed the most important info and at the end of the post are links to helpful sites and info if you choose to build your own. Here are some images of building a hydraulic press as well as a list of the parts I used. I Make This Press Machine Without Any Kind Of Welding.
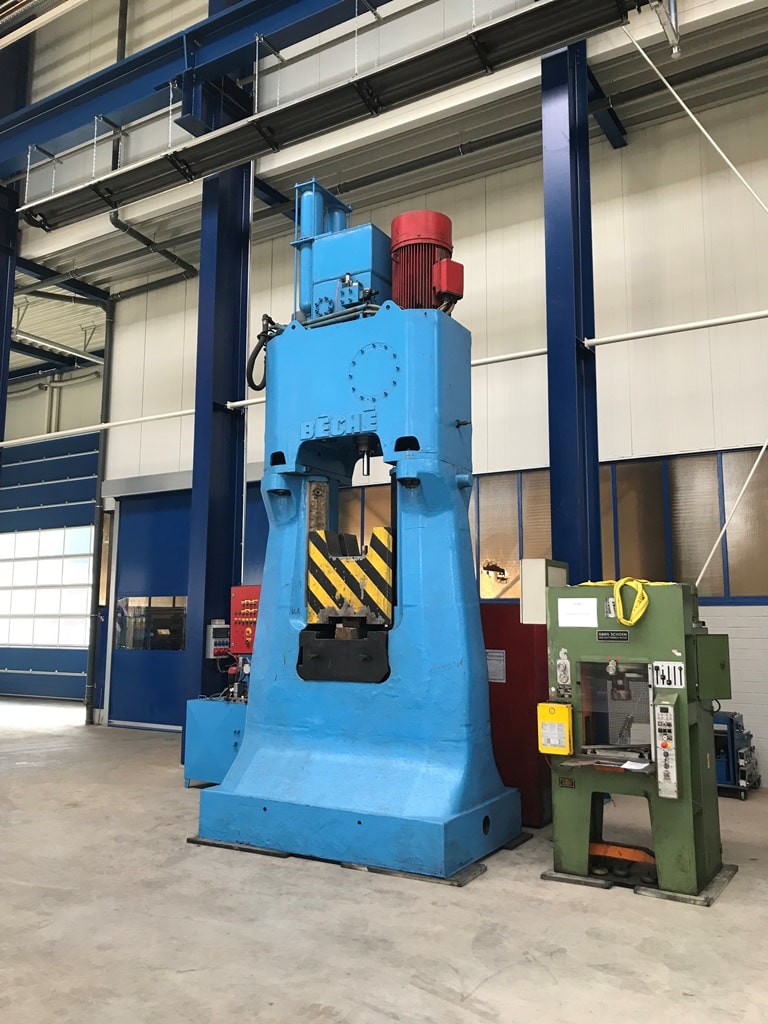
By Jim Batson Build Your Own Hydraulic Forging Press By Jim Batson This book and drawings are designed to help you build your own 24 ton Hydraulic Forging Press.
